BACKGROUND
Modern 3D printers can print intricate shapes at fine detail, but their low print speed enables them to only be used for prototyping or, at best, limited batch manufacturing. As an example, the fasted current metal printers can print a volume of about 60 cm³/hr. per nozzle or laser. This equivalent to about 8 grams/minute for a stainless-steel material. Cold spray is a manufacturing technique wherein particles, usually of metal, are accelerated at supersonic velocities to impact on a substrate. The high speed of the particles causes them to cold weld onto the substrate. Traditionally, this has been used to build up material onto broken parts so that that they could be re-machined before returning the part to service. Recently, organizations such as General Electric, Spee3D, and the National Research Council of Canada have developed 3D printers using cold spray techniques that are capable of enough precision to generate full 3D printed parts at speeds on the order of kilograms per hour. Each of these entities are using particles accelerated by high-speed air streams. While they can focus the streams well enough to generate parts, the precision is still relatively low, and the surface finish is poor compared to other 3D printing processes. This is because the air stream can only be focused so fine before coherence problems start to occur due to high back pressure, turbulence, and supersonic flow.
SUMMARY OF TECHNOLOGY
Current 3D printers can print in high resolution but tend to be slow. Some manufacturers are overcoming speed issues by using a cold spray technique that can discharge material at high flow rates. Unfortunately, the resolution of the print suffers due to limitation on the compactness of the supersonic air stream they use to entrain the powder grains making the print. OSU technology overcomes this limitation while maintaining the speed of the print by ionizing the powder grains. The ionized grains can then be accelerated, focused, and steered to high precision using electric and magnetic fields. The flow rate of the powder grains can also be tracked with high precisions using magnetic flow meters. Ionizing printer material particles similarly to the way paint powder is ionized in an electrostatic spray gun. Once ionized, the particles can then be accelerated by electric/magnetic fields and steered by electromagnetic fields like the way electrons are accelerated and steered in a CRT or a particle accelerator. They are then impacted on a grounded substrate where the part can be built up. Additionally, if it is desired to remove the particles from the flow stream for purposes such as increasing the accuracy/precision of the print then the electromagnetic yoke can turn the particles away from the air stream while a passageway channels the air away. This is like how an inkjet printer steers out unneeded ionized liquid printer toner into a gutter to be re-used. Any material that can be formed using a cold weld process and has powder than can be ionized is eligible to be used in this printing process.
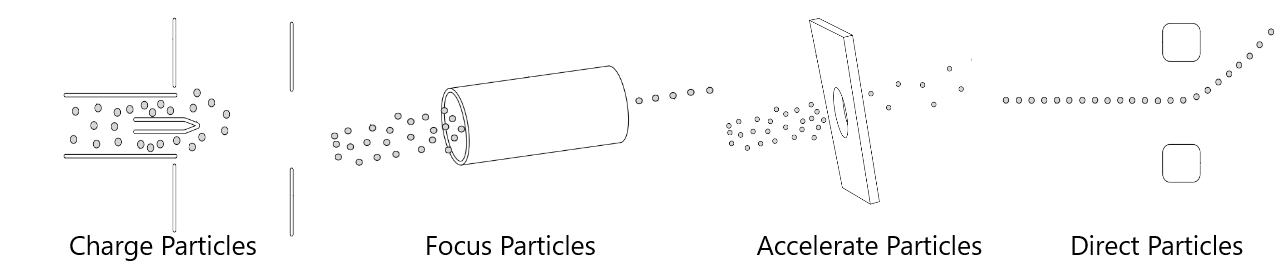
POTENTIAL AREAS OF APPLICATION
MAIN ADVANTAGES
- Increases the speed of printing
- High resolution and accuracy
- Isotropic finish
STAGE OF DEVELOPMENT
- There is a Proof of Concept for this technology.