BACKGROUND
Rapidly evolving unmanned aircraft system (UAS) requirements have necessitated the creation of novel methods to provide power to these craft in increasingly niche environments such as high altitudes or using more available heavy fuels to existing platforms to provide power to these craft, particularly with regards to turbogenerators. However, current turbine generators for hybrid aircraft are complex, and add volume and weight to the system. Additionally, the designs often employ a singular shaft, which forces generator to spin at high rotational speeds that are ideal for the turbine, resulting in large losses of power due to operation near the material limits of the device. These constraints create a clear need for novel designs to increase the performance, versatility, and efficiency in turboelectric power generation to meet ever-increasing demands for new applications.
SUMMARY OF TECHNOLOGY
Researchers at OSU have developed a concept of a novel configuration of an axial gas turbine turbogenerator. An exemplary embodiment of this is ducting exhaust from the outlet of a turbojet which then spins a secondary bladed rotor assembly radially coupled to a switched reluctance generator, solid induction generator, permanent magnet generator, or a combination of them. By radially “sharing” the rotor of the generator and turbine, the mechanical complexity, volume, and weight are all reduced. Additionally, the design allows for the main shaft and the generator rotor to rotate at different speeds, decreasing the amount of loss associated with operating near the material limit, a serious constraint of joint-shaft designs. Around this unit is the stator assembly and housing, which can be designed in a way to allow ambient air into/through it, making the engine stator more easily cooled and maintaining power generation efficiency. This easily retrofittable novel architecture can provide a much-needed performance and efficiency boost in power-generation for unmanned systems, compact aircraft, and compact ground-based power generation.
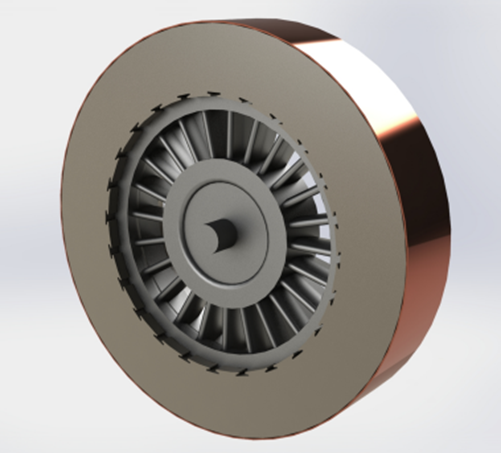
POTENTIAL AREAS OF APPLICATION
- Compact aircraft-based power generation
- Versatile unmanned aerial systems, particularly those at high-altitude
- Compact ground-based power generation
MAIN ADVANTAGES
- Reduction in mechanical complexity, volume, weight
- Able to run on heavy fuels such as diesel
- Easily retrofittable to existing engines
- More easily cooled engine stator
STAGE OF DEVELOPMENT